Table of Contents
A distributed control system is known as a DCS, is a computerized system that eliminate environmental and human risk by automating industrial machinery used in long and continuous processes. With increase in productivity and accuracy.
Many different industries use distributed control systems, such as transportation and processing, electric power generation, mining extraction, chemical manufacture, water and wastewater treatment and pharmaceutical processing facilities.
A control system is a collection of electrical or mechanical components that employs control loops and the feedback loop to govern other components or systems. Systems with all the hardware and software control functionalities required for measurements and modifications within a single process are called control loops. An essential component of industrial and process automation systems are control systems.
How does a distributed control system work?
Distributed control system are configured with the control loops. Computers, sensors, and controllers are some examples of these control loops. Every component has a distinct function, such as process control, data storage, or data gathering, trend building, scheduling, alert etc.
A DCS allows each and every component of a machine to have its own specialized controller that manages the operation, as opposed to a centralized control system that manages every unit.
In a plant, a DCS has multiple local controllers. The local controllers are connected by a fast communication ethernet network. Also each controller functions independently, an operator oversees central supervisory control.
Industrial control applications such as Supervisory Control and Data Acquisition (SCADA) and DCS share functional similarities. Power plants, the processing of oil and gas, telecommunications, transportation, and water and waste management all employ SCADA systems. They are all employed in scenarios where the control center is situated in a more isolated area.
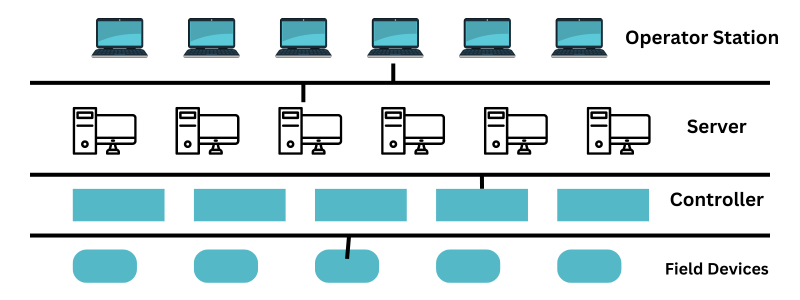
In a typical DCS setup, the system is comprised of several key components:
Controllers: These are the devices that execute control algorithms. Each controller manages a specific portion of the plant or process.
Field Devices: These include sensors, actuators, and other equipment that interact with the physical processes.
Communication Network: This network facilitates data exchange between controllers, field devices, and the central monitoring system.
Human-Machine Interface (HMI): The HMI provides operators with a graphical interface to monitor and control the system.
Data Historian: This component collects and stores process data for analysis and historical record-keeping.
The Architecture of DCS
The architecture of a DCS typically includes three hierarchical levels:
- Field Level: At this level, sensors and actuators interact directly with the physical process. Field devices collect real-time data and execute commands from the control system.
- Control Level: This level consists of distributed controllers that process data from the field level. Controllers perform calculations and execute control algorithms to maintain optimal operation.
- Supervisory Level: The highest level in the hierarchy, where the HMI and data historian reside. This level provides operators with a comprehensive view of the system, enabling them to make informed decisions and analyze historical data.
Benefits of Distributed Control Systems
Reliability and Redundancy: By distributing control functions across multiple controllers, DCS enhances system reliability. If one controller fails, others can take over, minimizing downtime and ensuring continuous operation.
Scalability: DCS can easily be scaled up or down depending on the needs of the process. New controllers and field devices can be added without disrupting the existing system.
Flexibility: The modular nature of DCS allows for easy customization. Different process areas can be managed independently, and changes to one part of the system do not necessarily affect others.
Improved Process Control: DCS provides real-time data and advanced control algorithms, which result in more precise and efficient management of industrial processes.
Enhanced Data Management: The integration of data historians and analytical tools allows for detailed analysis of process data, leading to better decision-making and process optimization.
Applications in Industry
Distributed Control Systems find applications in a variety of industries:
- Power Generation: In power plants, DCS manages everything from boiler control to turbine operation, ensuring efficient and stable electricity generation.
- Oil and Gas: DCS is used for monitoring and controlling extraction processes, refining operations, and distribution, helping to optimize production and maintain safety.
- Pharmaceuticals: In the pharmaceutical industry, DCS ensures the precise control of production processes, crucial for maintaining product quality and regulatory compliance.
- Manufacturing: From automotive to food and beverage manufacturing, DCS helps in managing complex production lines, enhancing efficiency and reducing waste.
Emerging Trends and Future Directions
The landscape of Distributed Control Systems is continually evolving, driven by technological advancements:
- Integration with Industry 4.0: The rise of Industry 4.0 brings with it advancements in IoT, big data, and artificial intelligence. DCS systems are increasingly being integrated with these technologies to enhance process monitoring, predictive maintenance, and autonomous operations.
- Cybersecurity: As DCS systems become more connected, cybersecurity becomes a critical concern. Advances in encryption and network security protocols are being developed to protect against potential cyber threats.
- Cloud Computing: The shift towards cloud-based solutions offers new opportunities for data storage, analysis, and remote monitoring. Cloud integration allows for more scalable and flexible control systems, with the potential for enhanced collaboration and real-time insights.
- Edge Computing: Edge computing brings processing power closer to the source of data generation, reducing latency and improving real-time control. This trend is complementing DCS by enabling faster decision-making and more responsive control.
- Enhanced User Interfaces: Modern HMIs are becoming more intuitive and user-friendly, incorporating advanced visualization techniques and virtual reality to improve operator interaction with the system.
Challenges and Considerations
While Distributed Control Systems offer numerous benefits, they also come with challenges:
- Complexity: The distributed nature of DCS can lead to increased complexity in system design and maintenance. Proper planning and configuration are crucial to avoid issues.
- Integration with Legacy Systems: Many industries still use legacy systems that may not be easily compatible with modern DCS. Integration solutions and careful planning are needed to ensure seamless operation.
- Cost: Implementing a DCS can be a significant investment. However, the long-term benefits of improved efficiency and reliability often outweigh the initial costs.
Conclusion
Distributed Control Systems are essential for todays industrial automation demands, offering a hardy, scalable and effective control solution that caters to diverse industries. DCS systems are getting upgrades to meet current demands as part of the continuous improvement brought by technology advances and Industry 4.0 prospects. It is by understanding and embracing these systems that we may improve process control, data management, and by extension operational efficiency in general. In today evolving process world, a properly done DCS system is a most powerful weapon / a strategic tool for the Industries to help them in their journey to implement the complexity of Automation as it finds today. It also speeds up its productivity with the progression of PLC & SCADA.
1 thought on “What is DCS (Distributed Control System)?”